Crushed, Bruised And Broken
An Interaction with SII Team and Leaders
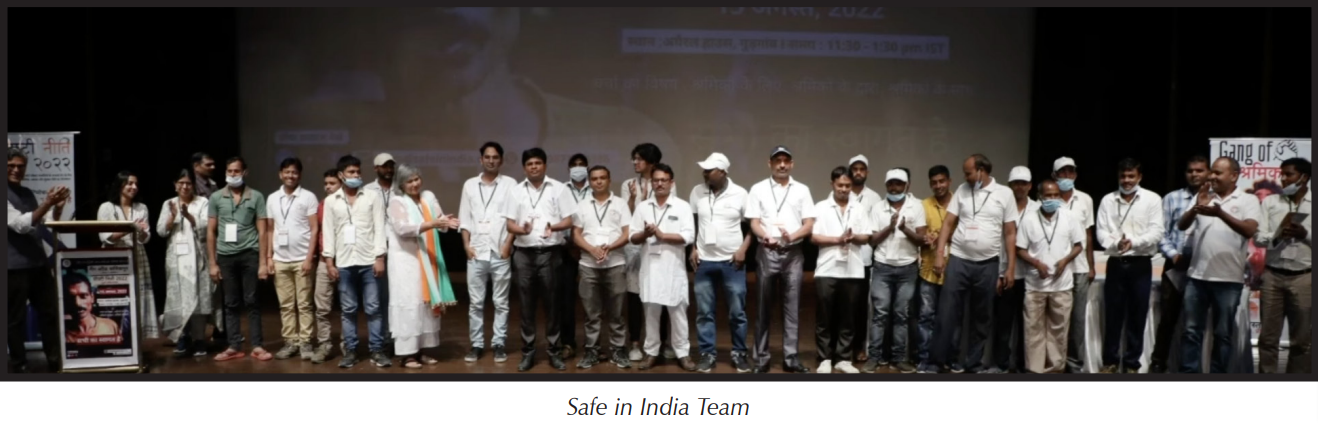
The third largest auto industry in the world functions with unsafe labour practices which are taking a brutal toll. Can it take steps to safeguard its worker’s health?
Common Cause team reached out to Safe in India leaders, Sandeep Sachdeva and Chitra Khanna and their wonderful team of young professionals, to understand more about their work and contributions. The excerpts of the interaction are given below.
Safe in India has been trying to get the Indian auto industry to pay more attention to occupational safety and health. It engages directly with auto workers and companies in order to raise awareness about OSH. In an interview with Common Cause, members of SII, including the Co-founder Sandeep Sachdeva and the Head of the Safety Initiative Chitra Khanna, discuss their work.
1. Let’s kick off the interview with a factoid from your website: 20 workers lose a finger or hand every day in Gurgaon’s auto hub. That’s a shocking statistic. How is this even possible, and why is this not more widely known?
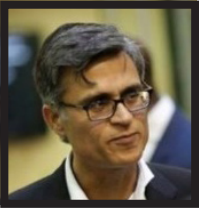
Sandeep Sachdeva (Co-founder, SII) : The reasons for these accidents are understandably complex, but at the root of them all is a poor safety culture and competitive pressures experienced by auto manufacturers, which result in a relentless chase for production at the lowest possible cost in their deep supply chain, disregarding worker safety and rights. This results in widespread non-compliance regarding adherence to Indian factory laws and international guidelines.
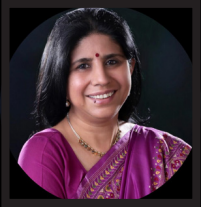
Chitra Khanna (Head of the Safety Initiative, SII) : As reported in the CRUSHED series of reports1 , worker accidents are under-reported. Official accident numbers are only a fraction of worker accidents, illnesses, and deaths nationally. This conceals the severity of the issue, and, therefore, most Indians do not know about the issue. Additionally, individual workers losing fingers or hands do not find a place in the news cycle, unlike fires or chemical leaks that are deemed newsworthy.
2. What is the figure for worker accidents in all the auto hubs in India?
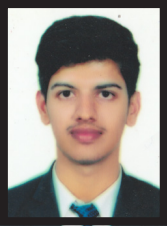
Ankit Singh (Systemic Change Executive, SII) : Such data is not available from any government or private source in India, but we know that these are in thousands every year. In Haryana alone, SII has found 5000+ such injured workers over six years, and this year we expect to find and help about 1,500 in just Haryana and Maharashtra. For CRUSHED 20222 , we identified 50 injured workers in other auto hubs of Tamil Nadu, Gujarat, and Karnataka within a period of one month, indicating that the total accidents nationally are probably 5,000+.
3. How did Safe in India come about? What was the impetus to start working among auto workers?
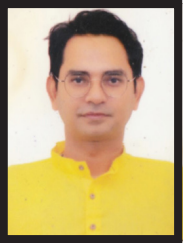
Masab Shamsi (Head-Worker Assistance Center, SII) : It started with a late 2014 media report, “Your car has been built on an assembly line of broken fingers”3 , which reported 20 cases of lost hands and/or fingers in automotive sector factories every day in just one ESIC (Employee State Insurance Corporation) hospital in Gurugram. To investigate further into this article, an assessment was conducted in 2015 with case studies of 20 individuals by three IIM Ahmedabad alumni and we found that the information in the article was indeed accurate and a majority were from auto sector suppliers. We have also observed that 60 percent of these accidents are related to power press machines which are widely used in the auto industry. So in March 2016, SII was formally launched, and our first Worker Assistance Centre was opened in December 2016 at Manesar, Gurgaon, a large auto sector hub for Maruti-Suzuki, Hero and Honda.
4. The backgrounds of the core team are interesting. You are an IIM graduate who worked in international finance and then quit to pursue your passion - Safe in India Foundation. How did you bridge these two, which lie at opposite ends of the spectrum? Would you advise other IIT-IIM graduates to forego corporate jobs and work in the social-impact space?
Sandeep : I quit the finance sector as I could not deal with the guilt of being part of the extreme form of capitalism we currently have, and which, I believe, continues to accelerate destruction of the environment and the human condition. It was then not difficult for me to start Safe in India, which has provided me an opportunity to do something, however small, in being part of the solution. The journey so far has been exciting, frustrating and fulfilling in equal measure.
I am no one to advise anyone to do what in their lives. I hope we all live with integrity with our values as much as we can. Corporate executives have the IQ and the power to contribute positively to the future of our world and all I would request is that they must not become slave to their job descriptions, but look up and look out at the world, and think hard about what their jobs are doing to people and nature and is that what they want to do for rest of their lives. They would be best at answering it to themselves and to their sons and daughters.
5. Can you break down the areas in which SII works: Worker compensation, improving workplace safety through advocacy and engaging with ESIC?
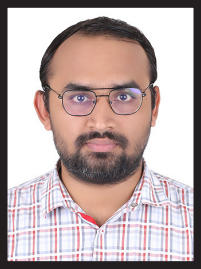
Dhanraj B (Consultant Project Manager, SII) : SII works across four inter-twined and well-defined pillars of activities to help Indian workers.
First, we have now supported 5,541 injured workers, in Haryana and Maharashtra to access better ESIC healthcare and compensation, of which 4,465 (nearly 80%) were injured in auto-sector factories.
Second, for improving workplace safety in the national auto-sector supply chain for more than a crore workers, we have been engaging with the top 10 auto-sector brands, their apex bodies (SIAM and ACMA) and the government. SII also publishes an annual series of reports4 : CRUSHED which focuses on worker accidents & SafetyNiti which focuses on the safety policies of the brands.
Third, to help more than three crore workers and their families, SII engages with ESIC regionally and nationally to improve ESIC’s healthcare and insurance compensation services. ESIC has issued more than 10 national notifications based on SII’s recommendations.
Fourth, for empowering workers through knowledge of ESIC and workplace safety, SII leverages in-person interactions like monthly worker support groups and at-scale outreach through social media. More than 2,500 workers have attended SII’s support group meetings. More than 55,000 workers now follow its Hindi Facebook page.
Our last annual review has a short summary and video of all our work: https://www.safeinindia.org/ post/2022-year-in-review-thanks-for-your-support-on-this-long-journey-to-sab-ka-saath-sab-ka-vikas
6. There are also trade unions that operate in auto hubs, including Manesar. Do you coordinate with them on issues of workers’ safety, advocacy etc?
Chitra :SII has tried to work with trade unions but it has not been successful. A major limitation of trade unions is that they largely represent permanent workers in the auto sector brands’ own factories. The CTU unions (Central Trade Unions) are non-existent in smaller MSMEs. Most temporary workers and workers in the supply chain (mostly MSMEs except some big brands of specialised components like air conditioning, music systems or raw material) of the auto sector brands are not part of any unions. Almost all reported accidents occur in the supply chain of the brands and not in the brands’ own factories. This limits our ability to work effectively with trade unions that operate in auto hubs.
7. What has your work at SII taught you about the structure of the auto-manufacturing industry in India?
Ankit : The auto-manufacturing industry in India is a multi-tiered value chain with auto brands at the top of the supply chain. Worker safety and other working conditions deteriorate as one goes down the supply chain. Most auto brands haven’t mapped their supply chain beyond the first tier and have minimum visibility of working conditions in the MSMEs/ industries constituting their deeper supply chains.
Auto brands’ guidelines and policies like the Supplier Code of Conduct are rarely applied to workers in the supply chain and contractual workers. Only a limited number of safety inspections and audits are conducted by the brands or by the government.
8. Are safety norms in the main plants and supply chains different? Can the norms in supply chains be tightened to prevent industrial mishaps?
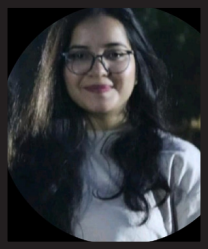
Shailja Tiwari (Systemic Change Executive, SII) : Safety norms aren’t the same for the brands’ own factories and the factories in the supply chain. For example, in our latest SafetyNiti report, we have reported how a majority of the top 10 auto brands still do not have a contractually binding Supplier Code of Conduct for their suppliers. Additionally, none of the brands appears to have an SOP or a comprehensive Occupational Safety & Health (OSH) implementation plan for their deeper supply chain.
Auto brands should take the lead in tightening the norms for improving safety measures and post-injury care for workers in their deeper supply chain. They have the best know-how, access to, and leverage over their own supply chains. Auto brands should map their deeper supply chains, make their safety policies and human rights policies contractually binding on their deeper supply chain, and monitor, audit, and report OSH parameters for their deeper supply chain to prevent industrial mishaps.
9. The auto industry contributes seven percent to India’s GDP and makes up half of manufacturing activity. It is structurally important for the economy. But at the same time it is exploitative and dangerous for workers. How does one reconcile the two?
Sandeep :In India, with poor working conditions in these factories, improving safety can be, we believe, profitable. They are not thinking harder about the cost of these accidents to businesses - both MSMEs in the supply chain and the brands - in lost time and production, quality, payments for losses, medical expenses, and repair and replacement of damaged machinery and equipment and indeed bribes. Obviously, these also have a negative impact on other workers.
Without improving working conditions, including occupational health and safety, we don’t see India replacing China under the China Plus One movement. Many of our businesses are thinking short-term jugaad, and cutting corners. At this rate, it will be difficult for the industry to continue to grow at the pace at which it intends, to achieve its 2030 Agenda for Sustainable Development, contribute to the ‘Sabka Saath, Sabka Vikas’ strategy and play a vital role in making India a $5 trillion economy.
Look at the improvement in Bangladesh’s garment industry’s professionalism, after the Rana Plaza incident, which changed the way 2,000+ factories worked for the better. That has been good for these businesses and the country. Can’t we do the same in our auto sector?
Sadly, this may happen more due to increasing pressure with new legislations like the European Commission’s corporate sustainability due diligence directive (which will be applicable very soon) and Japan’s thrust on human rights due diligence, requiring auditing and strengthening human rights in supply chains.
10. Can you talk a little bit about the Covid-19 relief that SII engaged in? Has auto industry employment picked up after the pandemic disruption?
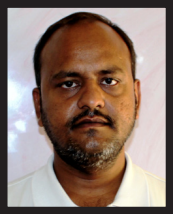
Amitesh Singh (Centre Coordinator - Worker Assistance Center, SII) : During the pandemic, we supplied 80 large oxygen tanks to ESIC Hospitals in Bihar, Karnataka, and Delhi catering to more than five lakh workers. We also distributed 450,000+ adult ration units, and 25,000+ masks, and helped 250+ workers get back home. We also helped 1,000+ workers get back into the job market by providing free vaccination in the Manesar community centre since many factories had made it mandatory for employment.
More strategically, we reported on the impact of the lockdown on workers’ jobs and wages and worked with ESIC to push for the Atal Bimit Vyakti Kalyan Yojana scheme (unemployment benefit) for wage loss compensation during the pandemic. SII contributed significantly to increasing disbursements from Rs 56 crores to Rs 80 crores since October 2021. We also helped 1,500+ workers apply to access this scheme.
Auto sector employment has reached pre-pandemic levels in most hubs. Immediately after the lockdowns were lifted, we observed that there was a shortage of workers, because they had gone back to their villages, the factory owners had even paid for the journey of the workers from their villages.
11. One of your reports states that the severity of injuries in factory accidents in Maharashtra is worse than in Haryana. Any reason why this may be?
Masab :We started working in Maharashtra’s auto sector hub of Pune in August 2022 and found more severe cases of crushed injuries compared to Haryana where we have been working for the last six years. In two months, we found more than 80 percent cases of lost fingers/ hands in Pune, while our Haryana figure indicates 67 percent finger/hand loss injuries. It would be necessary to conduct a thorough analysis to understand the specific reasons behind this, and this will take some time. However, we have found better ESIC compliance in Maharashtra. We are hopeful of doing a comprehensive analysis and understanding the cause before we publish CRUSHED 2023 later this year.
12. What happens to workers who lose a body part? Can they work again, where do they go?
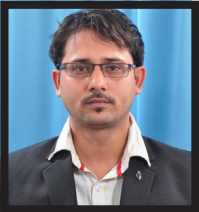
Manjeet Malik (Centre Coordinator - Worker Assistance Center, SII) : Many workers who lose a body part return to their villages or settle for lower-paying jobs like security guards which do not require the use of the lost limbs. Some injured workers do continue operating the same machine but at a lower wage. There are instances where workers have met with accidents multiple times on one machine, yet they operate the same machine.
Unemployment combined with the mental and physical trauma of the injury, high costs of residing in cities for treatment while many are not paid their salaries and a bureaucratic post-accident compensation process with ESIC, if they are ESIC-registered at all, pushes the vulnerable workers and their families further into despair.
Some employers promise the injured worker a permanent job, to keep them quiet until the heat of the issues subsides but end up breaking the promise. In CRUSHED5 , we have reported on multiple instances of workers who struggled with a powerful employer, often an unprofessional contractor (thekedaar), and bureaucracy, all of whom often do not empathise with and/or support the worker when needed.
13. The list of ESI-empanelled hospitals is extensive, and yet injured workers are often taken to non-ESIC private hospitals. What can be done to rectify this?
Datla Hari Varma (Associate, ESIC Initiatives, HR, & Accounting, SII) : : One of the major reasons for injured workers being taken to non-ESIC private hospitals is when the ESIC premium deducted from workers’ compensation is not deposited with ESIC, and therefore the workers are not even registered with ESIC. Possibly because of this, the injured workers are first taken to a private hospital, while ESIC paperwork is “completed” and then taken to ESIC hospitals often after one to three days of injury. To prevent this, better compliance with ESIC laws which state that workers are registered with ESIC immediately on joining, and premiums are deposited on time. Responsibility for this should lie with the auto sector brands and the government.
Also, currently, the admission process in ESIC hospitals is complicated with documentation from the employer required to injured workers for employment injuries. This can be simplified by the hospitals starting treatment first and collecting documents from the employer later.
14. India is looking to expand manufacturing and heavy industry. What kind of safeguards can be put in place to ensure worker safety?
Sandeep : We have been making several recommendations to the industry and the government.
For auto sector brands, we have been making our Top five policy and Top five operational recommendations to the auto sector brands that cover better OSH policies and implementation for their supply chain, e.g. do their boards even discuss working conditions in their supply chains? Do they monitor them and act when needed or have they just passed their cheaper and/or dirtier work to suppliers and abrogated their social responsibility that they claim?
The central and state governments need to implement laws better. For example, they need honest accident reporting and inspections, support MSMEs in improving their safety measures, and increase transparency on exemptions from factory- inspections. For workers, they should introduce practical policies and mechanisms for safety training, make OSH rules & information accessible to workers, and set up a confidential helpline for workers. They can also partner with OEMs/Brands to improve safety in ancillaries in the deeper supply chains.
Chitra: The labour department should create a working committee to work towards minimising accidents in industries to improve the condition of workers, strengthening institutional partnerships and actions to prevent accidents in supply chain’s MSME factories and meeting the international commitments of SDG 8 (specifically indicator 8.8), ILO labour standards, and the UN Human Rights Convention. The government should extend the requirement of Business Responsibility and Sustainability Reporting (BRSR) to large unlisted MNCs and ensure the adoption of BRSR Lite for MSMEs and supply chain companies.
15. What would you like our readers to do to help this cause of Indian workers?
Sandeep :I would urge all readers to write to their car or two-wheelers’ brands and ask them about the actions they are taking to improve the working conditions of their Tier 1,2,3 suppliers and prove it. They can also write to the state or central government, and even to their friends in the media. We would be grateful if they copied us at team@safeinindia.org.
I would also request them to register on our website www.safeinindia.org so we can update them regularly and to send us any thoughts and suggestions at the same email team@safeinindia.org
Endnotes
- The series of reports can be accessed here https://bit.ly/44ufi5b
- Safe in India (2022). CRUSHED 2022. Retrieved May 10, 2023 from https://bit.ly/3O6O9hx
- Sharma, Supriya (December 01, 2014). Your Car Has Been Built On An Assembly Line of Broken Fingers. Scroll.ini>. Retrieved May 10, 2023 from https://bit.ly/473COYw
- Supra Note 1
- Supra Note 2
NEXT »