Safe In India
Journey Since the Birth of the Organisation
Susmita Saha*
It was the winter of 2014 when a news item posted in the WhatsApp group of an Indian Institute of Management (IIM) alumni group triggered an intense debate. The article by Supriya Sharma1 of Scroll. in laid bare how “crush” injuries were taking place with alarming regularity in the automobile industry in Haryana. Twenty cases every day at a single hospital!
The article was titled “Your car has been built on an assembly line of broken fingers” and was initially greeted with scepticism and
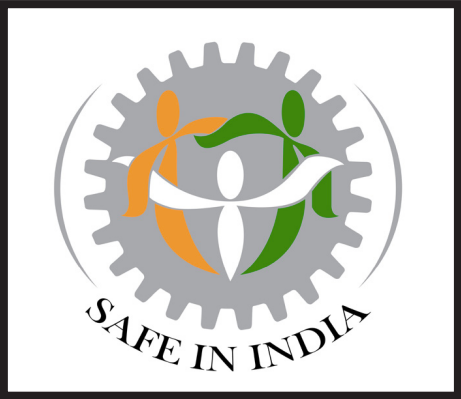
incredulity. But it also led to a debate about whether the dreadful figures quoted could be true. The alumni of the 1991 batch had people who were now in senior management positions at investment banks, consultancy firms and large corporates around the world. They had gained material success and some were thinking of “giving back” to society. The article was the right catalyst.
It was at this point that three of the alumni, Sandeep Sachdeva, Prabhat Agarwal and Ravi Gulati, decided to “look into this”. Sachdeva was a banker with HSBC Plc in the UK and in his mid-40s. Agarwal was founder and coach at Aravali Scholars where students from lower income backgrounds were mentored and provided with academic resources. He was also a known face in Gurgaon, which is one of the largest auto manufacturing hubs in India. Gulati had founded a number of social enterprises that focused on youth and education. Together they founded Safe in India (SII), through which they hoped to make a difference to the lives of auto-sector workers who suffered shop floor injuries or were vulnerable to them.
In September 2015, the three, in collaboration with a Gurgaon-based NGO called Agrasar, released a comprehensive report2 based on 20 case studies of workers who had suffered workplace injuries. This report, which focused on factory accidents and the post-injury phase where workers often had to fend for themselves, was a significant milestone in their efforts to understand occupational safety and health.
Born in early 2016, SII started by partnering with Udaipur-based Ajeevika Bureau to understand how to run a successful social enterprise. Financial accounts were submitted to Ajeevika for audit and their administrative procedures were adopted. The Rajasthan NGO, which works on livelihoods and labour rights, mentored the young social sector start-up for three years.
SII can be described as a collective of well-wishers who care about the well-being of workers in the Indian automobile sector and are dedicated to bringing about systemic change. India is among the top three or four automobile manufacturing countries in the world. The auto sector contributes roughly seven percent to the country’s GDP which comprises half of Indian manufacturing and employs tens of millions of workers. However, many of the workers are unskilled and have limited awareness about their rights and benefits. Moreover, the auto-sector is made up of auto companies and their supply chains. The companies (such as Maruti-Suzuki, Honda, Hero, TVS) assemble vehicles in their factories with parts that they source from their Tier-1 suppliers, who in turn get raw materials from Tier-2 suppliers and so on. The supply chain could have as many as four to five tiers, with the bottom rung comprising small parts workshops known to work mostly as sweatshops. For instance Maruti-Suzuki has 475 Tier-1 suppliers, while the Tier-2 may be four times that number3 . The auto companies claim that they are not even aware of who makes up the tail of their supply chains!
Accidents like crush injuries and hacked limbs occur because providing training to unskilled labour or adding safety measures to heavy machinery may raise the cost of production. And it is not just male workers who are injured. SII has documented numerous instances of female workers who have suffered from injuries, especially from power press machines. SII’s work has revealed that 90 percent of autosector workers are migrants, 65 percent have work contracts that are precarious, 50 percent are under 30 years and 65 percent have lost fingers or hands. And yes, 20 workers do lose their limbs every day, just in Gurgaon.
Over time, SII has evolved four “pillars of action” to address shop floor injuries. The first is assisting injured workers get employee state insurance, which is their statutory right. SII has assisted more than 2,500 workers get ESIC compensation. The second is improving workplace safety in auto manufacturing, with a focus on the supply chain, by engaging with the auto companies, industry associations and governments. The third pillar is to improve ESIC’s healthcare and compensation system nationally by engaging with the government body that pays out the insurance. They provide recommendations based on their experience of helping workers. The final pillar is to increase awareness about occupational safety and health (OSH) by engaging with workers.
During the COVID-19 lockdown, SII temporarily repurposed their services to support workers around Manesar. As factories stopped production and workers lost their homes and income, the organisation distributed over 450,000 adult ration packs and 25,000 masks. It also helped workers get back home.
SII publicises its work through reports and is now expanding from its home base of Gurgaon to other autohubs across the country like Pune, Chennai, Karnataka and Uttarakhand. The organisation is able to raise resources from corporate donors as well as the IIM and IIT-Roorkee alumni networks of the founders.
Endnotes
- Sharma, Supriya (December 01, 2014). Your Car Has Been Built On An Assembly Line of Broken Fingers. Scroll.in. Retrieved May 15, 2023 from https://bit.ly/473COYw
- Agrasar, Safe in India (2015). What Can Safeguard Workers? Retrieved May 15, 2023 from https://bit.ly/43Ca4TF
- Shared by Safe in India Team
NEXT »